Comelz Skiving Machines
Skiving Machines - The Comelz SS20 Computerised System
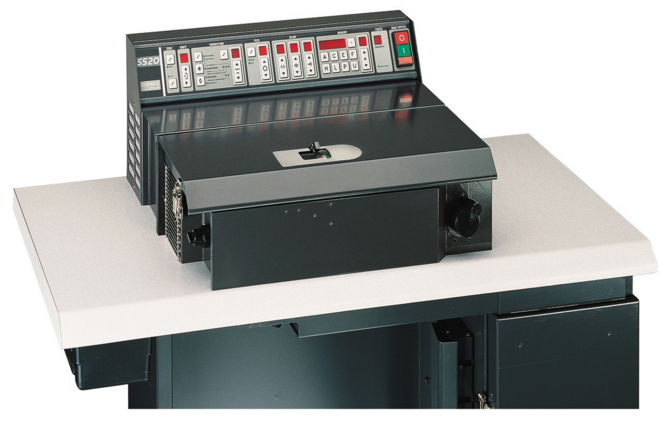
The SS20 was born out of the need for an accurate skiving machines using a combination of modern mechanicals coupled with the latest electronic technology. In a major departure from the traditional systems, the computer installed in the SS20 has made it possible to introduce some unique features.
Skiving Machines that look after themselves?
The machine, in fact, is constantly monitored, adjusting itself automatically to stay perfectly efficient while in operation. All functions are performed by mechanical units driven by independent motors operating under the direct control of the computer. The original structure of mechanical units has made it possible to use a tilting electro-spindle, thus allowing an immediate accessibility to mechanical parts and an easier knife and grindstone replacement. The console can be easily reached and the data displays are very clear. An efficient dust collector is built in the frame of the machine.
Knife Positioning, Sharpening and Grindstone Dressing
The gap between the cutting edge and the presser foot is preset by the operator with micrometric precision. An automatic device enables this gap to be maintained by moving the knife forward as it wears out. This very important automatic device provides for the maintenance of a high level of skiving efficiency and avoids frequent and possibly inaccurate adjustments.
These two operations, which in traditional machines cause a remarkable loss of time, are automatically performed by the machine, according to the parameters chosen by the operator (pressure, duration and interval). It is also possible to have the machine performing continuous sharpening for special skiving works. The operator can activate and deactivate knife sharpening and grindstone dressing at any time as needed.
Work Piece Feeding
The feed roller turns, by choice of the operator:
- continuously, at a speed preset by the operator
- at a variable speed, controlled by a pedal.
In both cases the work feeding speed can be very accurately set and it is not influenced by the thickness and toughness of the material being processed.
These features make the skiving of complicated work pieces very easy.
A knee operated switch lifts the presser foot to instantly release the work piece.
SKIVING
Skiving parameters:
- thickness
- width
- angle
- feed speed
are shown on a display and can be micrometrically adjusted.
The operator adjusts skiving parameters and the data is automatically stored in memory, in the activated section.
There are two scarf width guides:
- movable
- fixed
Both are present at the same time and can be alternately used on the same work piece.
The movable guide allows a fine adjustment of the scarf width. It is possible to program its disappearance under the work area to allow the use of the fixed guide.
This guide, positioned under the presser foot near the knife, is perfect for complicated skiving and for work pieces with very tight curves.
Any presser foot wear is compensated for automatically for every scarf, to guarantee constant skiving quality.
Skiving Machines with Data Storage
Uniquely our skiving machine has a memory for 800 different types of scarf (100 groups of 8) and each one is immediately accessible, all that is needed is a press of a button to recall the required type of scarf.
The operator can improve or modify the current scarf parameters configuration at any time. The new adjustment is stored in memory, replacing the former data.
For those work-pieces whose profile requires different skiving styles it is possible to program in a working sequence.
The operator has only press recall on the sequences display for the required types of scarf. Afterwards, just a slight pressure on the pedal will make the machine shift from one configuration to the next.
It is also possible to store these sequences in memory, making use of the ample and versatile memory of the machine.
For more information on this range of machines Click Here or call one of our specialists on 01933 359359