
Our Compressors can really take the pressure!
We were asked by a major shoe manufacturer to supply a compressor suitable for four ATOM Knife Tables and also the 80metres of solid air pipework structure around the production area. We were glad to help.
Read More on this story.
Cutting Systems UK provide all the maintenance both reactive and preventative on all the compressor systems and accessories we sell.
Compressed Air Systems.
After selling nearly 100 ATOM FlashCut Knife Cutting systems, many of our customers have asked for complete package solutions from us, Cutting Systems can now offer in-house, specialist maintenance, installation, and aftersales service on compressed air systems.
Our customers can now benefit from Cutting Systems being able to design and build complete production cells with Knife Cutting Systems and Compressed Air Systems, but we can also combine the annual service in the same visit. This saves money with only one planned maintenance visit – and that simplifies the Admin as well.
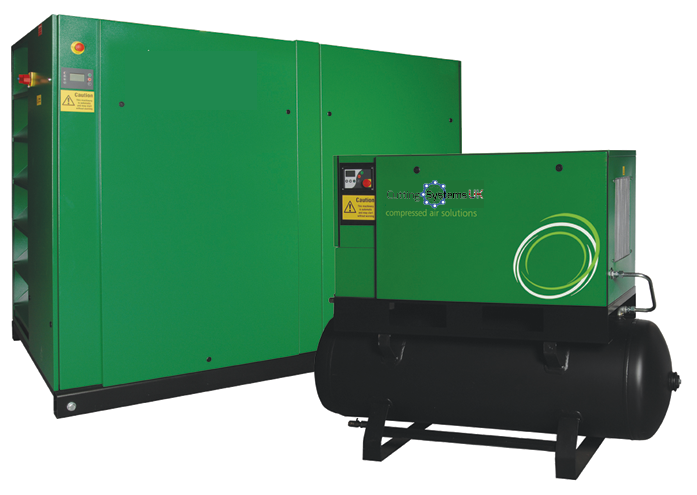
Advantages of Full Feature Compressors
Efficiency: High efficiency motors are used throughout the range offering less consumed power than standard motors.
Design: The compressors have been developed for ease of maintenance and reliability. The compressors can also be serviced from the front allowing them to be positioned against a wall.
Low Noise: Extremely low noise operating levels allow positioning of compressors within the work place, even in the immediate vicinity of personnel.
Manoeuvrability: The complete range of Avelair compressors have specifically designed holes for forklifts enabling ease of installation.
Low Maintenance: Careful placement of service items allow for ease of maintenance and reduction in costs
Reliability: High quality compressors suitable for all industrial and automotive applications.
Full Aftercare: Compressors are built in the UK offering a full Technical, Service and Sales backup.
We offer 3 sizes:
- 2.2kW for ATOM Knife Tables using only Electrical Cutting Chucks
- 7.5kW for ATOM Knife Tables, Single Pneumatic Cutting Chuck’s for all Standard Machines
- 11kW for ATOM Knife Tables, Twin Installations, for customer operating two machines within the same cutting cell’s.
Model | Motor | Capacity 8 bar | Capacity 10 bar | Receiver size optional | Built on dryer / filters optional | ||
---|---|---|---|---|---|---|---|
EDN 2.2 | 2.2kW | 10 cfm | 34 m3/hr | 15 cfm | 26 m3/hr | 250L | yes |
EDN 7.5 | 7.5kW | 39 cfm | 66 m3/hr | 33 cfm | 56 m3/hr | 250L | yes |
EDN 11 | 11kW | 58 cfm | 99 m3/hr | 49 cfm | 83 m3/hr | 300L | yes |
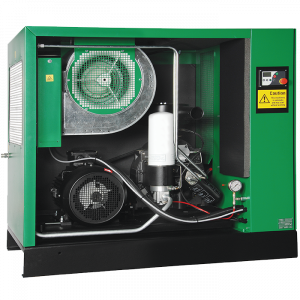
Our compressors are of the highest standard as standard. We supply them complete with:
- Auto drains that only drain when there is water in the tank, not just every 15mins regardless. This saves energy for the compressor and auto drain.
- Our compressors come with built in driers as standard which is required for the ATOM Knife table to operate to the best of their ability and also enable long life of many components.
- Built-In condensate unit, separating the oil and water from the auto drain fluids, a legal requirement now is to discard oil into any water ways. Our separators mean the water discharged can legally be disposed of using fowl waste, the toilet. The oil discharged is collected and disposed of by our own engineers upon each service of the system.
- In-Line AutoDrain Filters, to further ensure the removal of any large particles that could possibly be transferred into the compressed air system
We mainly only supply these compressors for our own Knife Cutting Systems, but can upon application provide a wide range of compressed air systems, and solutions.
Many of our existing customers are using our experience to add our own auto drains, driers, condensate management systems and filters to their existing compressed air systems to ensure that the ATOM Knife Cutting Systems are not damaged in anyway by excessive water in the compressed air supply.
For information on any of these systems or complete turnkey production lines please CONTACT one of friendly experts who will be happy to help.
Condensate Treatment Systems
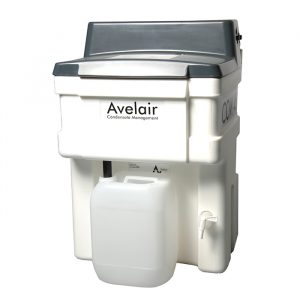
The Avelair condensate Oil Water Separation system is used for the collection and purification of oil-contaminated water, which is created by almost all compressed air systems, to the legal discharge limits. The Avelair range covers compressed air systems up to 7000 m³/hr.
Refrigerant Dryers
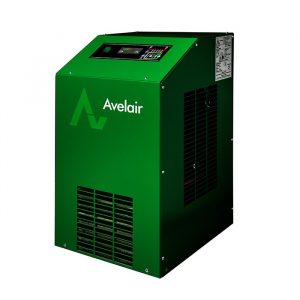
The Avelair Refrigerant compressed air dryers are high quality, self contained units ready for installation.
The units are designed to lower the dewpoint of the compressed air to 3°C to remove water carry over and to prevent contamination of the compressed air system.
They are available in sizes 1 m³/hr to over 2000 m³/hr and are fitted with environmentally friendly gas. As the air passes through the dryer, it is cooled by a refrigerant. Cold air holds less water vapour than warm air, so as the air cools, the water vapour condenses into liquid water. The air is heated back up to system temperature before re-entering the system in order to prevent any condensation in the pipes and the equipment downstream.
Zero Loss Condensate Drains
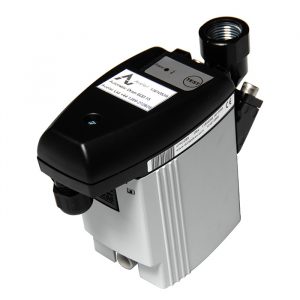
Avelair offer a range of high quality and robust zero loss condensate drains which can be installed on filters and air receivers to automatically discharge any condensate.
Compressed Air Filtration
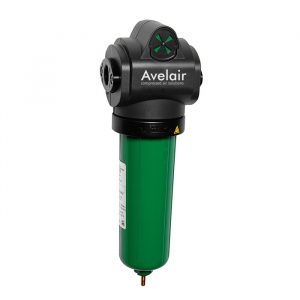
Avelair’s compressed air filters are robust and offer low pressure drops whilst ensuring oil removal from 25 micron down to 0.01 micron. These are available in a range of sizes from 1/2″ up to 4″.
The Avelair range of air filters are designed for high quality filtration of compressed air or gas in a wide of applications. The total filter design concept of the filter combines high performance, greater efficiency, ease of use, flexibility, and safety. The high performance is achieved by the flow-optimized filter design, paired with innovative filtration technology; this reduces pressure loss by 50% compared to conventional filters.
The unique bayonet lock ensures that the filter cannot be opened under pressure for increased safety. You will find greater energy savings are achieved by the timely replacement of a used filter element. This is determined by the Economizer (optional) that continuously measures the different pressures. An integrated microprocessor evaluates the measurement data and compares the higher energy costs caused by pressure loss with the costs of a new filter element. The series is available in nine sizes, six filter element types, and perfectly meeting all industrial air purification application requirements.
Cutting Systems UK provides all the maintenance both reactive and preventative on all the compressor systems and accessories we sell.